Double Side Thermoelectric Separation Copper Base PCB For Beauty Manicure UV Light
- 54 Views
- 30 Jan 2024
- Customer Background
- Cooperation Needs
- Technical Difficulties and Process Issues
- Solution
- Cooperation Effect
Double Side Thermoelectric Separation Copper Base PCB For Beauty Manicure UV Light
Circuit Layers: 2 Layers
Manufacture Type: Thermoelectric Separation
Substrate Thickness Tolerance: ± 10%
Front/Back/Multilayer Alignment Accuracy: 0.1mm
Application: Beauty UV Lighting System
Customer Background
Mulinsen is a company specializing in the production of UV LED lamps, which are mainly used in industrial, medical, and other fields. Mulinsen's products have very high requirements for circuit boards, which require high thermal conductivity, high anti-interference, and high precision.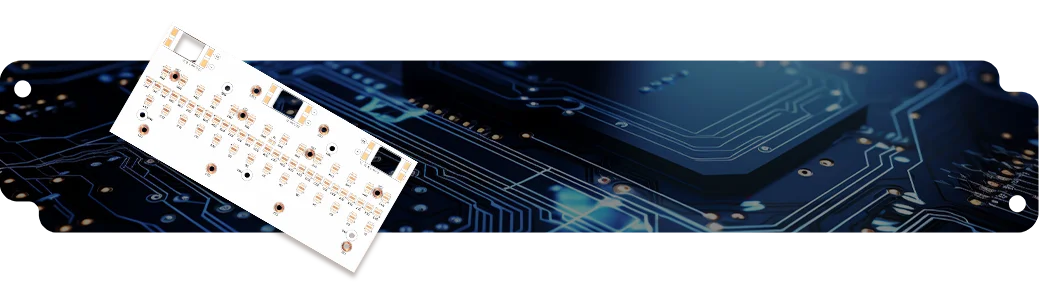
Cooperation Needs
Mulinsen originally used ordinary FR4 circuit boards, but found that under the high-power working environment of UV LED lamps, the heat dissipation performance of FR4 circuit boards was insufficient, which could easily cause the circuit board to overheat and affect the brightness and life of the lamp. At the same time, the anti-interference performance of the FR4 circuit board is not ideal, and it is easily interfered by external electromagnetic signals, affecting the control and adjustment of the lamp. Mulinsen hopes to find a circuit board material more suitable for UV LED light applications that can effectively solve the problems of heat dissipation and anti-interference.Technical Difficulties and Process Issues
In the production process of metal-based circuit boards, the production of countersunk holes is an important link, which can realize the multi-layer connection of circuit boards and improve the density and function of circuit boards. However, there are also some technical difficulties and process problems in the production of countersunk holes, mainly as follows:The use of special plates with high TG, high speed, high frequency, and thick copper increases the difficulty of drilling roughness, drilling burrs, and drilling dirt. The hardness of these special plates is relatively high, which causes greater wear on drill bits. This can easily lead to rough drilling surfaces, burrs on the edges of the drilled holes, and impurities such as copper shavings in the drilled holes, which affect the quality and reliability of countersunk holes.
There are many layers, the cumulative total copper thickness and plate thickness make it easy to break the tool when drilling. The total copper thickness and plate thickness of high-rise circuit boards are relatively large, which requires high rigidity and strength of the drill bit. It is easy to generate large torque and pressure when drilling, causing the drill bit to break or deform, affecting the accuracy and efficiency of drilling.
Due to the thickness of the plate, it is easy to cause oblique drilling problems. The thickness of the high-rise circuit board is relatively large, and the drill bit is prone to deflection when drilling, resulting in inaccurate position and direction of the countersunk hole, affecting the interlayer connection and signal transmission of the circuit board.
Solution
To address the technical difficulties and process issues in the production of metal-based circuit boards, we have adopted the following solutions:Ⅰ: Choose the appropriate drill material and parameters.
For special plates with high TG, high speed, high frequency, and thick copper, we choose high-quality tungsten steel drill bits, which have the characteristics of high hardness, high wear resistance, and high-temperature resistance, and can effectively reduce drilling roughness and drilling burrs. and the difficulty of removing dirt. At the same time, we optimize the drill bit’s rotation speed, drop speed, coolant, and other parameters according to different plate materials and hole diameters to ensure the quality and efficiency of drilling.
Ⅱ: Use step-by-step drilling and front and back drilling methods.
For the total copper thickness and board thickness of the high-level circuit board, we adopted a step-by-step drilling method, that is, first drill a shallow hole with a large-diameter drill bit, and then drill a deep hole with a small-diameter drill bit, which can reduce Torque and pressure during drilling, reducing the risk of easily breaking the drill. At the same time, we adopt the method of front and back drilling, that is, first drill from one side to half, and then drill from the other side to the other half. This can reduce the problem of oblique drilling during drilling and improve the accuracy and alignment of drilling.
Ⅲ: Using high-precision drilling machines and alignment systems.
In response to the board thickness and inter-layer alignment requirements of high-rise circuit boards, we use a high-precision drilling machine and alignment system, which has high speed, high stability, and high accuracy, and can effectively control the position and direction of drilling. Ensure the quality and reliability of countersunk holes.
Cooperation Effect
We have provided customers with the production service of a batch of metal-based circuit boards with countersunk holes. After testing and verification by customers, we found that our solution can effectively solve the technical difficulties and process problems encountered in the production of countersunk holes, improving the quality and reliability of circuit boards. Customers are very satisfied with our quality, give us high praise and trust, and decide to establish a long-term cooperative relationship with us and entrust us to produce more orders for them.
Double Side Thermoelectric Separation Copper Base PCB, pcb,
Related Blog
- LED Lighting
- Double Sided Separation Copper Core PCB For High Temperature Testing Equipment System
- Double Sided Copper Core PCB Design For Industry Machine
- Multilayer Copper Core PCB For Electronic Machine
- Single Sided Copper Substrate PCB Design For Dynamo System
- Multilayer Double Sided Aluminum Core PCB Design For Machine
- Single Sided 2 Layers Thermoelectric Separation Copper Core PCB For Testing Equipment
- Single Sided Aluminum Based PCB Board For High Bay Light System
- Thermoelectric Separation Copper Core PCB Design For Cooling System
- Mirror Aluminum Base PCB For Plant LED Light
- Double Sided Aluminum Core Through Hole PCB Rapid Prototype For Indoor Plant Grow Lighting
- Single Sided Thermoelectric Separation Copper Base Printed Circuit Board For High Bay Light
- Nickel Plated Multi-layers Copper Core Board For Growing Lighting System
- Single Side Aluminum Core PCB Fabrication For Hotel Lighting System
- Single Sided Copper Base Ciricuit Board Design For High Bay Light
- Single Sided Al Substrate Printed Aluminum Circuit Board For Hotel Lighting
- Single Sided Aluminium Based PCB Fabrication For Hotel Interior LED Lighting
- Single Sided Aluminum Core Circuit Board Design For Hotel Lobby Lighting
- Mass Production Single Sided Aluminum Base PCB Board For Hotel Ceiling Light
- Single Sided Al Base PCB Rapid Prototype For Hotel Lighting