Thermoelectric Separation Copper Core PCB Design For Cooling System
- Views
- 30 Jan 2024
Thermoelectric Separation Copper Core PCB Design For Cooling System
Circuit Layers: Single Side Copper Base+Double Side FR4
Product Unit Size: 1000*450mm
Substrate Thickness Tolerance: ±10%
Element Size Tolerance: ±0.15mm
Base Material: C1100
Base Material Thickness: 0.8-5.0mm
Customer Background:
Founded in 2001 and headquartered in Livonia, Michigan, our customer Visotek Inc. is a leading innovator in the development and manufacturing of chiller equipment. With core competencies in various refrigeration equipment technologies, Visotek Inc. is able to meet the needs of various industries and excels particularly in the field of medical refrigeration manufacturing.Client Needs:
Faced with the challenges associated with optimizing the thermal performance of chillers, Visotek Inc. sought innovative solutions to improve the cooling efficiency and thermal management of their systems. They needed a reliable supplier that could provide a one-stop solution for single-sided double-layer thermoelectrically separated copper core PCB.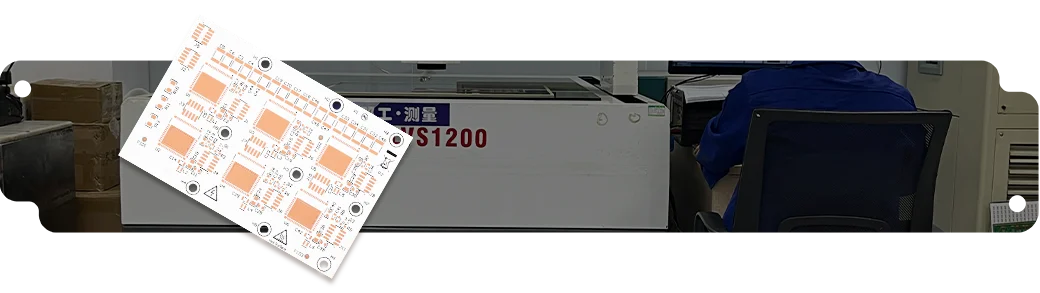
Solutions Provided:
Our company is a well-known PCB manufacturer and supplier, providing one-stop solutions to meet the requirements of our customers:Ⅰ: Thermoelectric Separation Technology: Utilizing the most advanced thermoelectric separation technology, we create a single-sided double-layer copper core PCB that can effectively manage and dissipate heat.
Ⅱ: Copper Core Construction: The use of copper cores ensures excellent thermal conductivity and thus optimal heat dissipation within the cooling machine.
Ⅲ: Process Control: Our engineers work closely with customers to strictly control the process to produce PCBs that integrate seamlessly with customers' cooling systems. This involves incorporating specific thermal vias and optimizing circuit layout to enhance thermal performance.
Ⅳ: One-stop Solution: From the initial discussion and negotiation to the final production stage, we provide a comprehensive one-stop solution. This streamlined process simplifies procurement and integration for customers.
Collaboration Process:
This collaboration involves ongoing communication and coordination between our engineering team and the client’s technical experts. Prototypes are developed and tested to ensure the custom PCB meets the customer's thermal and thermal stability specifications.Results And Feedback:
The delivered single-sided double-layer thermoelectrically separated copper core PCB demonstrated significant improvements in the customer's cooler equipment:Ⅰ: Enhanced Thermal Performance: The advanced PCB efficiently manages heat, helping to improve the thermal performance and overall efficiency of your cooling system.
Ⅱ: Reliable Operation: Custom design ensures the cooler operates reliably even in challenging thermal conditions.
Ⅲ: Simplified Integration: The one-stop solution simplifies the integration process for customers, reducing the time and effort required for procurement and assembly.
Prospect:
This successful collaboration laid the foundation for an ongoing partnership. The customer expressed interest in exploring additional PCB solutions for future iterations of its chiller equipment, demonstrating the potential for continued collaboration and mutual success.
Thermoelectric Separation Copper Core PCB, MCPCB,
Related Blog
- LED Lighting
- Double Sided Separation Copper Core PCB For High Temperature Testing Equipment System
- Double Sided Copper Core PCB Design For Industry Machine
- Multilayer Copper Core PCB For Electronic Machine
- Single Sided Copper Substrate PCB Design For Dynamo System
- Multilayer Double Sided Aluminum Core PCB Design For Machine
- Single Sided 2 Layers Thermoelectric Separation Copper Core PCB For Testing Equipment
- Single Sided Aluminum Based PCB Board For High Bay Light System
- Thermoelectric Separation Copper Core PCB Design For Cooling System
- Mirror Aluminum Base PCB For Plant LED Light
- Double Sided Aluminum Core Through Hole PCB Rapid Prototype For Indoor Plant Grow Lighting
- Single Sided Thermoelectric Separation Copper Base Printed Circuit Board For High Bay Light
- Nickel Plated Multi-layers Copper Core Board For Growing Lighting System
- Single Side Aluminum Core PCB Fabrication For Hotel Lighting System
- Single Sided Copper Base Ciricuit Board Design For High Bay Light
- Single Sided Al Substrate Printed Aluminum Circuit Board For Hotel Lighting
- Single Sided Aluminium Based PCB Fabrication For Hotel Interior LED Lighting
- Single Sided Aluminum Core Circuit Board Design For Hotel Lobby Lighting
- Mass Production Single Sided Aluminum Base PCB Board For Hotel Ceiling Light
- Single Sided Al Base PCB Rapid Prototype For Hotel Lighting