Why Always Use Aluminum PCB In LED Application Instead of Copper or Ceramic PCB?
- Views
- 05 Apr 2024
- What Are Aluminum PCBs, Copper PCBs and Ceramic PCBs?
- Do MCPCB dissipate heat?
- Do mcpcb lightweight for led lights
- Cost-effectiveness
- Final Words
In our daily lives or workshops, aluminum PCBs are commonly used in various LED lights including swimming pool LEDs, street lights, stage lights, car headlights, office lights, and LED strip lights. Selecting the appropriate material is crucial, particularly in LED technology where efficiency and performance are key considerations. Among the various options available, why prefer to use aluminum PCB instead of copper core PCB or ceramic PCB which has higher thermal conductivity value? Let Best Technology answer it for you.
What Are Aluminum PCBs, Copper PCBs and Ceramic PCBs?
At the present, there are total three kinds of high thermal conductivity PCBs in the PCB manufacturing - aluminum PCB, copper core circuit board and ceramic PCB board. Among them, aluminum and copper PCB belong to metal core PCB and ceramic PCB is a special one that made by ceramic substrate. Founded in 2006, focusing on electronics & circuit board industry, Best Technology provide a one-stop service from designing, DFM, and fabrication of all types of Metal core PCB (from 1-layer, 2L, Double sided, Multi-layer to SinkPad PCB), to components purchasing, Metal core circuit board assembly and box building assembly. We also provide ceramic PCB fabrication suitable solution for our customers that help to save time & money of them, and then become the most reliable supplier of them.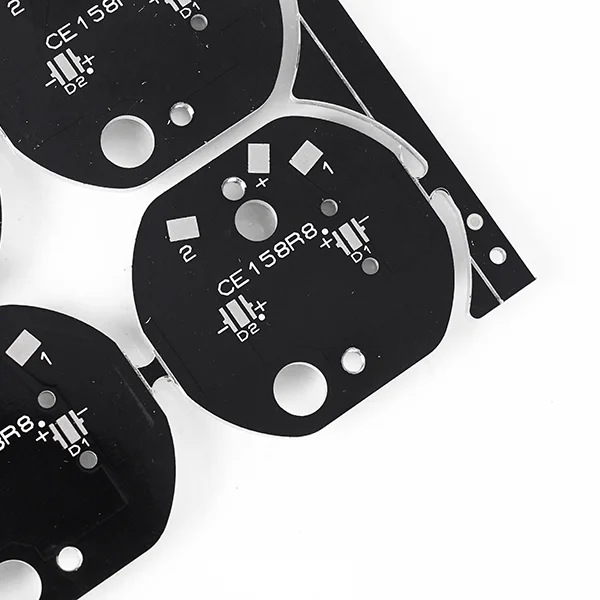
What Are Advantages of Aluminum PCBs in LED Applications?
Though ceramic substrate circuit boards and copper-clad based PCB have numerous benefits than aluminum core led pcb, but why designers or engineers prefer to use aluminum PCB as the core material in LED lights? Keep reading then you may find the answers!Do MCPCB dissipate heat?
At the beginning, aluminum is not the critical part for a LED. You know, active components generate significant heat during operation, and some engineers will use a cooling fa on devices to achieve the head dissipation. But when temperatures are excessively high, relying solely on active cooling measures will typically only cooling the surface temperature of devices while the internal temperature still very high. Therefore, they searching for a material that can replace the cooling fan and efficiently dissipate the heat in short time. Then, they found the aluminum PCBs are literally made for LED lights.Aluminum PCB is made by aluminum substrate and consist of a layer of aluminum core, a dielectric layer and trace layer. The aluminum base is on the bottom side and can directly touch the devices, and depends on the thermal conductivity of dielectric layer, the heat can be effectively and uniformly dissipated away from active components.
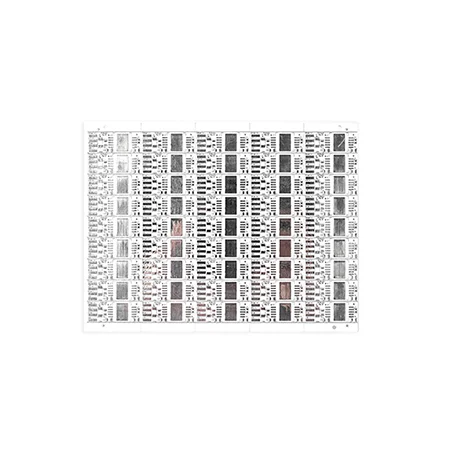
Do mcpcb lightweight for led lights
Actually, aluminum core circuit board is not the lightest board among the three thermal management PCBs, but obviously it is lighter than copper substrates. Why not use ceramic PCB? Because it has much expensive price, complex manufacturing and longer lead time. And copper core PCB is heavier and rigidness, may resulting the overall weight of the whole product. Especially most of LEDs are install on the high place, copper has potential risk for safety. Therefore, aluminum is the go to choice for LED application. And last but not important, the lightweight of aluminum PCBs not only simplifies handling and installation but also reduces shipping costs, contributing to overall cost savings.Cost-effectiveness
As previously mentioned, aluminum PCBs provide a cost-effective solution without compromising product performance. The lower cost of raw materials and simplified manufacturing process make aluminum PCBs economically option for LED applications, especially in large-scale production. Additionally, since most LED lights are designed to operate at 5V, 9V or 12V, aluminum PCBs can meet this voltage requirement effectively. Therefore, choosing an aluminum core PCB is highly recommended for LED applications that require lower power.Real-world Applications of Aluminum PCBs in LED Technology
Aluminum PCBs find widespread use in the lighting industry, powering a diverse range of LED products, including:Streetlights
Automotive lighting
Spotlight
Swing pool RGBW LED
Indoor and outdoor displays
Residential and commercial lighting fixtures
The superior thermal management capabilities of aluminum PCBs have been instrumental in enhancing the efficiency and longevity of LED lighting systems, resulting in significant energy savings and environmental benefits.
As LED technology continues to evolve, so does the demand for innovative solutions in PCB manufacturing. In the case of aluminum PCBs, ongoing research and development efforts aim to further enhance thermal conductivity, reduce production costs, and improve overall performance, ensuring that they remain the preferred choice for LED applications in the future.
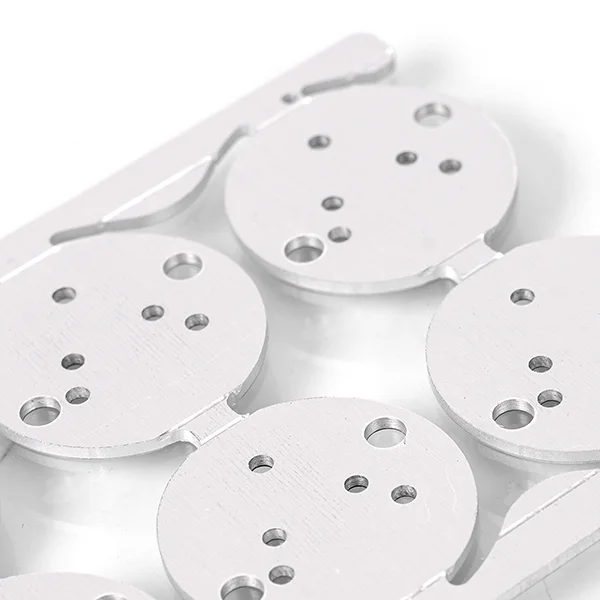
Final Words
In a word, the selection of the right PCB material is crucial for ensuring the optimal performance and longevity of LED applications. While copper and ceramic PCBs have their merits, aluminum PCBs emerge as the preferred choice due to their superior thermal conductivity, cost-effectiveness, and compatibility with LED technology. With advancements in manufacturing techniques and ongoing research, aluminum PCBs are poised to continue driving innovation and efficiency in the field of LED lighting. By means of ODM, OEM and DFM one stop service, we welcome all the questions and inquiries about metal core PCB, we will reply to you immediately when receive your RFQ, and give you the best quotation within 12 hours. Meanwhile, our professional engineering will give you design support and technical service specialized for your flexible.Aluminum PCB, LED, Application, Ceramic PCB,
Related Blog
- What is Thermal and Electrical Separating Pad in Metal Core PCB?
- LED PCB Assembly Process: Step-by-Step Guide for Beginners
- Why Always Recommend White Solder Mask Black Silkscreen for Aluminum PCB?
- What Materials Are Commonly Used for Manufacturing Lighting PCBs?
- Everything You Should Know About Metal Core Circuit Board
- What Are the Differences Between Ceramic PCB, Metal Core PCB And Standard FR4 PCB?
- Why Choose Best Technology As Your MCPCB Manufacturer?
- What is LED Light Circuit Board and How to Make it?
- When is International Labour Day in 2024 and What are the Significances of It?
- How Does A Convexity Comes Out On Thermoelectric Separation Copper Based PCB?
- Why is Aluminum LED PCB Important for Indoor Growth Lights?
- Application of Metal Core Pcbs in the Development of LED Technology
- Why Choose White Solder Mask for Metal core PCB When Used In LED Devices?
- Understanding Aluminum LED PCBs in 1000w LED Grow Lights
- What Are the Advantages of Metal Core PCB? How to Choose?
- Automotive Light Copper Core Pcb Production Process—testing
- Why Are Metal Core PCBs, Especially Copper Core, Used In Heat-Sensitive Electronics?
- How do aluminum LED PCBs improve LED efficiency?
- What Are the Differences Between Regular and Thermoelectric Separation Copper-Base PCBs?
- Aluminum PCB VS FR-4 Performance Comparison