Why It Says Aluminum PCB is the Key Part of the Audio Equipment?
- Views
- 31 Jan 2024
Aluminum PCBs are perhaps the most common metal-based PCBs among all printed circuit boards except the standard FR4 PCB. They consist of an aluminum core as the base/substrate of the board, laminated with a thermal layer, to achieve efficient heat dissipation. This enables all components on the circuits to lower temperatures and enhance overall performance.
Due to its excellent performance and efficiency, aluminum PCBs find widespread applications in electronics, the commons are audio equipment, automobiles, computers, and various other fields. In this article, we will discuss what aluminum PCBs are and their key benefits when used in audio equipment.
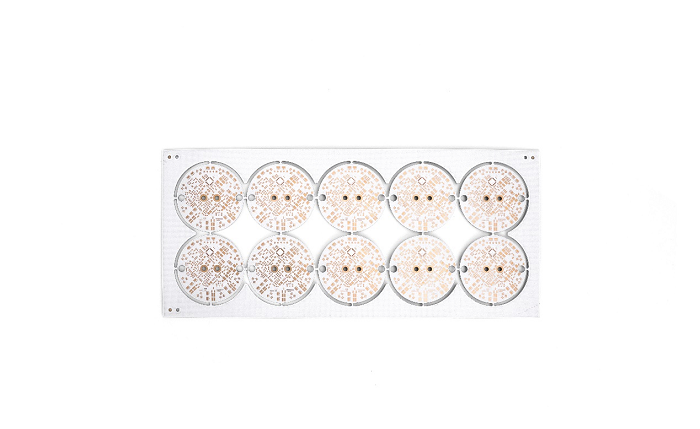
In fact, aluminum's excellent thermal dissipation capacity makes it extremely useful for cooling devices where it is employed. By effectively dissipating heat, aluminum helps devices maintain an optimal temperature, thereby enhancing their overall performance. This ability to regulate temperature is crucial, especially in electronics and other applications where excessive heat can degrade performance, shorten component lifespan, or even cause malfunctions. Aluminum's combination of thermal conductivity and resistance makes it a valuable material for improving the efficiency and reliability of various electronic systems and devices.
1. Aluminum Core: The central component of an aluminum PCB is the aluminum core itself. This core provides mechanical stability to the board and serves as a highly efficient heat conductor for dissipating heat generated by the components mounted on the PCB.
2. Dielectric Layer: Above the aluminum core, there is a dielectric layer, often made of materials like epoxy or polyimide. This dielectric layer acts as an electrical insulator, preventing short circuits and providing electrical isolation between the components and the aluminum core.
3. Copper Foil Layer: On top of the dielectric layer, copper foil traces are etched to create the desired circuitry. These copper traces serve as the conductive pathways for electrical signals to travel between components on the PCB. The copper foil layer is laminated onto the dielectric layer using a bonding process.
4. Solder Mask: A solder mask is applied over the copper traces to insulate them from environmental factors and prevent unintended solder bridges during the soldering process. The solder mask also provides protection against corrosion and helps improve the PCB's overall reliability.
Aluminum PCB, mcpcb led board, aluminum core pcb,
Due to its excellent performance and efficiency, aluminum PCBs find widespread applications in electronics, the commons are audio equipment, automobiles, computers, and various other fields. In this article, we will discuss what aluminum PCBs are and their key benefits when used in audio equipment.
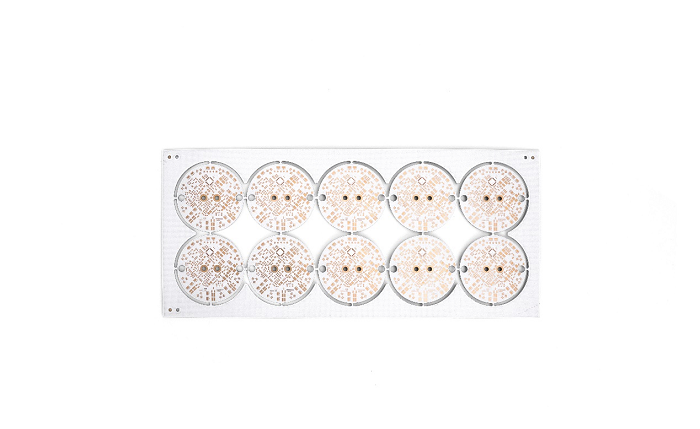
What Is Aluminum PCB and Its Basic Structure?
An Aluminum PCB, or aluminum-based printed circuit board, is a type of PCB that utilizes an aluminum core as its foundation instead of the traditional FR4 or other substrate materials.In fact, aluminum's excellent thermal dissipation capacity makes it extremely useful for cooling devices where it is employed. By effectively dissipating heat, aluminum helps devices maintain an optimal temperature, thereby enhancing their overall performance. This ability to regulate temperature is crucial, especially in electronics and other applications where excessive heat can degrade performance, shorten component lifespan, or even cause malfunctions. Aluminum's combination of thermal conductivity and resistance makes it a valuable material for improving the efficiency and reliability of various electronic systems and devices.
What Is the Basic Structure of Aluminum PCB?
In general, an aluminum PCB typically consist of three layers, and add two coating layers.1. Aluminum Core: The central component of an aluminum PCB is the aluminum core itself. This core provides mechanical stability to the board and serves as a highly efficient heat conductor for dissipating heat generated by the components mounted on the PCB.
2. Dielectric Layer: Above the aluminum core, there is a dielectric layer, often made of materials like epoxy or polyimide. This dielectric layer acts as an electrical insulator, preventing short circuits and providing electrical isolation between the components and the aluminum core.
3. Copper Foil Layer: On top of the dielectric layer, copper foil traces are etched to create the desired circuitry. These copper traces serve as the conductive pathways for electrical signals to travel between components on the PCB. The copper foil layer is laminated onto the dielectric layer using a bonding process.
4. Solder Mask: A solder mask is applied over the copper traces to insulate them from environmental factors and prevent unintended solder bridges during the soldering process. The solder mask also provides protection against corrosion and helps improve the PCB's overall reliability.
5. Silkscreen: Lastly, a silkscreen layer may be added for labeling components, indicating polarity, or providing other relevant information about the PCB assembly. The silkscreen layer is typically printed on top of the solder mask.
Why Aluminum PCB Is Important for Audio Equipment?
It can be said, aluminum PCBs play a crucial role in audio equipment, particularly in amplifiers, preamplifiers, and other audio components. Here are three main contributions of aluminum PCBs in audio devices:1. Heat Dissipation
Aluminum PCBs are excellent at dissipating heat generated by electronic components, including transistors and integrated circuits (ICs). In audio equipment, especially high-power amplifiers, managing heat is critical to maintaining component efficiency and longevity. Aluminum PCBs with their thermal conductivity help dissipate heat efficiently, preventing overheating and potential damage to sensitive components.2. Compact Design
Aluminum PCBs allow for a more compact and lightweight design compared to traditional FR4 PCBs (made from fiberglass). This is particularly advantageous in audio equipment where space is often limited. The ability to integrate components closely together on aluminum PCBs enables manufacturers to design more compact and aesthetically pleasing audio devices without compromising performance.3. Electromagnetic Interference (EMI) Shielding
Aluminum PCBs offer improved electromagnetic interference (EMI) shielding compared to standard PCB materials. EMI can introduce unwanted noise or interference in audio signals, degrading sound quality. Aluminum PCBs help mitigate EMI issues by providing a shielded environment for sensitive electronic components, resulting in cleaner audio output.
Aluminum PCB, mcpcb led board, aluminum core pcb,
Related Blog
- What is Thermal and Electrical Separating Pad in Metal Core PCB?
- LED PCB Assembly Process: Step-by-Step Guide for Beginners
- Why Always Recommend White Solder Mask Black Silkscreen for Aluminum PCB?
- What Materials Are Commonly Used for Manufacturing Lighting PCBs?
- Everything You Should Know About Metal Core Circuit Board
- What Are the Differences Between Ceramic PCB, Metal Core PCB And Standard FR4 PCB?
- Why Choose Best Technology As Your MCPCB Manufacturer?
- What is LED Light Circuit Board and How to Make it?
- When is International Labour Day in 2024 and What are the Significances of It?
- How Does A Convexity Comes Out On Thermoelectric Separation Copper Based PCB?
- Why is Aluminum LED PCB Important for Indoor Growth Lights?
- Application of Metal Core Pcbs in the Development of LED Technology
- Why Choose White Solder Mask for Metal core PCB When Used In LED Devices?
- Understanding Aluminum LED PCBs in 1000w LED Grow Lights
- What Are the Advantages of Metal Core PCB? How to Choose?
- Automotive Light Copper Core Pcb Production Process—testing
- Why Are Metal Core PCBs, Especially Copper Core, Used In Heat-Sensitive Electronics?
- How do aluminum LED PCBs improve LED efficiency?
- What Are the Differences Between Regular and Thermoelectric Separation Copper-Base PCBs?
- Aluminum PCB VS FR-4 Performance Comparison